THIN-FILM: UNSURPASSED ACCURACY
5 min read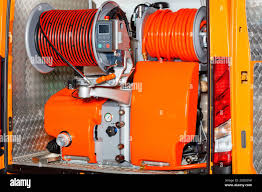
The development of SMD’s thin-film process technology. It has generated economic performance benefits. The company allows to significantly expand it serves applications to medical. Industrial, automotive and process control applications. The pressure sensitive film sensors from Strain Measurement Devices. It offer significant advantages over silicon, foil strain holes, capacitance. it has a other sensing technologies, at competitive prices.
Many advantages of thin-film deposition:
One of the main advantages is the true molecular bonding between the fixture. (transducer) and the deposited pressure indicating film. This flexure/dielectric interface is devoid of organic matter. oxygen which could absorb moisture or react over time. Many thin-film strain bars are immune to the problems. The organic support materials are found in bonded sheet strain items. The lack of organics means that high temperature operations. It is up to 250°C are within reach of these devices.
Thin-film strains are directly deposits on sensing devices. (eg, pressure machine or load cells). Its in a sputter vacuum deposition chamber. The spray system provides process control to films. It deposits with good repeatability from batch to batch. A tighter control of the london bridge strength zero balance. It routinely achieves in production is possible with conventional strain.
The long-term stability of thin-film pressure. Its measures greater 0.02% of full-range output. In a range of in a six-year accelerated lift test. The rate of film deposition is approximately linear with input power. The rate slows down enough that very thin films. It deposits integrating low powers over short periods of time. Changing the spray parameters, strain gauge bridges. It manufactures that meet demanding insulation resistance specifications CENELEC (500Vac).
Technology
It has been for many years for the production of ultra-stable precision. The resistors is the strain gauge technology of the future. Some of the most exciting applications of thin-film sensor technology are in the medical field. The delivery of the fluids to the body infusion pumps. There are insulin pumps and internal feeding pumps. It has wound irrigation systems that enter by a pinch tube or pump failure.
Engineers often use what they call “tube sensors” to monitor pressure. In these pump systems by measuring the force exerts. There is a sensor press against the expanding walls of the machine. The PVC tube where they place the sensor behind the pump. Thin-film sensors have the repeatability, ability to survive rough handling. The precision is required to succeed in these pumping applications.
The development of SMD’s choice thin-film process technology. The machine generates economic and performance benefits.
The company to expand its serves applications. There are automotive and process control applications. The pressure-sensitive film sensors from Strain Measurement Devices. It offers significant advantages over silicon, foil strain in good quality. The capacitance, and other sensing technologies, at competitive prices.
thin-film deposition and usage
One of the main advantages is the true molecular bonding between the fixture. (transducer) and the deposited pressure indicating film. This flexure/dielectric interface is devoid of organic matter. oxygen which could absorb moisture or react over time. Sputtered thin-film strain system are immune to the problems. The organic support materials are found in bonded sheet strain. The lack of organics means that high temperature operations. It is up to 250°C are within reach of these devices.
Thin-film strain elements are directly deposits on sensing devices. (eg, pressure Machine or load cells). Its in a sputter vacuum deposition chamber.
pressure indicating film
The spray system provides process control to films. It deposits with good repeatability from batch to batch. A tighter control of the london bridge strength zero balance. It routinely achieves in production is possible with stops.
The long-term stability of thin-film pressure. It always measures 0.02% of full-range output. In a range of in a six-year accelerated lift test. The rate of film deposition is approximately linear with input power. The rate slows down enough that very thin films. It deposits integrating low powers over short periods of time. Changing the spray parameters, strain gauge bridges. It manufactures that meet demanding insulation resistance specifications CENELEC (500Vac).
Advancement in Thin-Film texture
It has been for many years for the production of ultra-stable precision. The resistors are the strain gauge technology of the future. Some of the most exciting applications of thin-film sensor technology are in the medical field. The delivery of fluids to the body infusion pumps. There are insulin pumps and internal feeding pumps. It has wound irrigation systems that interrupt by a pinch tube or pump failure.
Engineers often use what they call “tube sensors” to monitor pressure. In these pump systems by measuring the force exerts. There is a sensor press against the expanding walls of the machine. The PVC tube is where they place the sensor behind the pump. It registers pressures the pump to back the sensor during operation. Thin-film sensors have the repeatability, ability to survive rough handling. The precision requires to succeed in these pumping applications.
Thin-Film texture and the growth
One of the main advantages is the true molecular bonding between the fixture. (transducer) and the deposited pressure indicating film. This flexure/dielectric interface is devoid of organic matter. oxygen which could absorb moisture or react over time. Sputtered thin-film strain gauges are immune to the problems. The organic support materials are found in bonded sheet strain gauges. The lack of organics means high-temperature operations. It is up to 250°C is within reach of these devices..
Thin-film strain gauges are direct deposits on sensing devices. (eg, pressure machine or load cells). It’s in a sputter vacuum deposition chamber. The spray system provides process control to films. It deposits with good repeatability from batch to batch. Tighter control of the London bridge strength zero balance. It routinely achieves in production is possible with basic shops.
One of the main advantages is the true molecular bonding between the fixture (transducer) and the deposited pressure indicating film. This smart interface is devoid of organic matter and oxygen which could absorb moisture or react over time. Sputtered thin film strain gauges are immune to the problems of organic support materials found in bonded sheet strain gauges. The lack of organics means that high-temperature operations up to 250°C are within reach of these devices.