MACHINING CENTERS: HORIZONTAL OR VERTICAL?
3 min read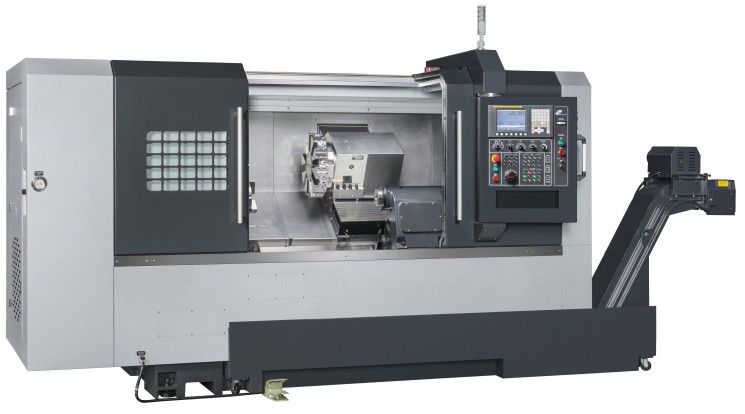
The decision to have a horizontal or vertical CNC machining center is important
Your factory is ready to expand. Should you add another vertical machining center or invest in a horizontal one?
To answer that question, you’ll need to take a good look at where your business is today and where you plan to go with a new machine purchase.
Think about the customers you have now and the ones you want in the future. Consider what you really need the machine to do in terms of production, accuracy and installation goals. When it comes to pricing, remember to factor in all costs outside of the initial machine purchase, including tools, software, training, maintenance and repairs.
1 . PRICE
The prices of a Horizontal Machining Center can be daunting at first impression. Factories need to make additional investments in software, tool management systems and inspection equipment to achieve maximum return on investment. Long-term productivity gains outweigh these additional costs, but cash flow management is crucial in the implementation phase.
As an alternative, a Vertical Machining Center costs about half as much as a Horizontal, and a factory that installs a new, additional Vertical will be able to use existing technology and tools. When capital is scarce or cash flow is slow, a Vertical Machining Center is probably the best choice.
2. QUALITY
As mentioned before, despite programming a Horizontal to be longer and complicated, it is possible to machine more difficult and intricate parts. In addition to the construction of a Horizontal Machining Center it is made to be more robust than a Vertical one. Tools vibrate and deflect less, making the machine easier to machine and last longer, before parts or the machine itself need to be replaced.
Productivity is also a point that favors Horizontal Machining Centers, as it can machine up to twice as fast as a Vertical, in most jobs. This means that over time, the higher price is offset by superior productivity.
3. YOUR CUSTOMERS
Verticals are generally easier to set up, so a factory with many small customers who place small orders for volume parts will be able to move on to the next job more quickly. These machines are also the best choice for working with large plates. In addition, because they are more common, there are more people trained to program and operate a Vertical.
Horizontal Machining Centers have fewer configurations and can also use more than one tool at the same time. Rotating pallets mean the machine is never idle. Programming is complex and setup takes longer, but more difficult parts can be produced faster and more accurately. Factories that produce long orders or complex parts will have greater gains from a CNC lathe machining center.
4. WORK
Verticals are more common in auto repair shops, so operators and programmers are more likely to be familiar with the controls. For jobs that require a high level of precision, experienced technicians will need to perform every setup.
A factory purchasing its first Horizontal Machining Center will certainly need to invest in training to maximize the machine’s return as it is more difficult to use and fewer workers have experience with them. Programmers must be skilled, however the machine needs little input from operators once it starts up. With a single Horizontal, it is possible to do the work of two or more Verticals, so a plant may need fewer staff members overall.